產(chǎn)品中心PRODUCTS
服務(wù)熱線
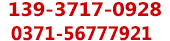
正文
當(dāng)前位置:首頁 > 新聞中心 > 行業(yè)動態(tài) > 正文硅磚
配料時適當(dāng)增加亞硫酸紙漿廢液的含量;往模型內(nèi)裝料時,要將邊角泥料按實,保證邊角的致密;磚坯脫模后,往干燥板上堆放前,應(yīng)在干燥板上墊棉布條或報紙,同時磚坯之間保持5〜10mm的距離;運(yùn)輸過程中防止振動過大而使磚坯產(chǎn)生缺邊掉角現(xiàn)象。
硅磚成型時如何減少磚坯尺寸公差?
成型前應(yīng)檢查錘頭的平整度和偏斜度,防止錘頭不平或偏斜;成型前還要檢查成型臺與出磚器的平整度,使錘頭與上模板相適應(yīng);成型后應(yīng)對磚坯逐塊檢尺,保證坯體符合尺寸公差要求。
硅磚磚坯在干燥過程中產(chǎn)生裂紋的原因硅磚在干燥過程中產(chǎn)生裂紋的主要原因是干燥溫度升高過快,或受熱不均勻,在磚坯內(nèi)造成過大的蒸汽壓,致使坯體開裂。因此,制訂合理的干燥制度,嚴(yán)格管理,嚴(yán)格操作,可減少干燥過程中產(chǎn)生裂紋的現(xiàn)象。
—般采用什么干燥器干燥硅磚磚坯?
干燥硅磚磚坯一般采用隧道干燥器,有的中、小廠采用干燥室或干燥炕進(jìn)行干燥。用隧道干燥器可以干燥各種硅磚磚坯。機(jī)械成型的焦?fàn)t硅磚磚坯可以裝在干燥車上直接推入干燥器內(nèi)進(jìn)行干燥,干燥后的殘余水分一般控制在1〜2%,用手工成型或振動成型的大型、異型磚坯,應(yīng)先在干燥室內(nèi)干燥1〜3d后,再送入干燥器進(jìn)行干燥,其殘余水分應(yīng)控制在1%以下。
燒成硅磚時應(yīng)注意的問題
600℃以下可用較快而均勻的升溫速度燒成。700〜1200℃因磚坯體積變化不大,強(qiáng)度逐漸提高,可盡快升溫。1200〜1430℃的高溫階段,是SiO2晶型轉(zhuǎn)化和體積變化階段,升溫速度應(yīng)逐漸降低,并應(yīng)緩慢而均勻地升溫。為此,可采用弱還原焰燒成。燒成以后的冷卻階段,600℃以上可以快冷,600℃以下應(yīng)緩慢冷卻。燒成升溫速度(參考值)如下:
配料時適當(dāng)增加亞硫酸紙漿廢液的含量;往模型內(nèi)裝料時,要將邊角泥料按實,保證邊角的致密;磚坯脫模后,往干燥板上堆放前,應(yīng)在干燥板上墊棉布條或報紙,同時磚坯之間保持5〜10mm的距離;運(yùn)輸過程中防止振動過大而使磚坯產(chǎn)生缺邊掉角現(xiàn)象。
硅磚成型時如何減少磚坯尺寸公差?
成型前應(yīng)檢查錘頭的平整度和偏斜度,防止錘頭不平或偏斜;成型前還要檢查成型臺與出磚器的平整度,使錘頭與上模板相適應(yīng);成型后應(yīng)對磚坯逐塊檢尺,保證坯體符合尺寸公差要求。
硅磚磚坯在干燥過程中產(chǎn)生裂紋的原因硅磚在干燥過程中產(chǎn)生裂紋的主要原因是干燥溫度升高過快,或受熱不均勻,在磚坯內(nèi)造成過大的蒸汽壓,致使坯體開裂。因此,制訂合理的干燥制度,嚴(yán)格管理,嚴(yán)格操作,可減少干燥過程中產(chǎn)生裂紋的現(xiàn)象。
—般采用什么干燥器干燥硅磚磚坯?
干燥硅磚磚坯一般采用隧道干燥器,有的中、小廠采用干燥室或干燥炕進(jìn)行干燥。用隧道干燥器可以干燥各種硅磚磚坯。機(jī)械成型的焦?fàn)t硅磚磚坯可以裝在干燥車上直接推入干燥器內(nèi)進(jìn)行干燥,干燥后的殘余水分一般控制在1〜2%,用手工成型或振動成型的大型、異型磚坯,應(yīng)先在干燥室內(nèi)干燥1〜3d后,再送入干燥器進(jìn)行干燥,其殘余水分應(yīng)控制在1%以下。
燒成硅磚時應(yīng)注意的問題
600℃以下可用較快而均勻的升溫速度燒成。700〜1200℃因磚坯體積變化不大,強(qiáng)度逐漸提高,可盡快升溫。1200〜1430℃的高溫階段,是SiO2晶型轉(zhuǎn)化和體積變化階段,升溫速度應(yīng)逐漸降低,并應(yīng)緩慢而均勻地升溫。為此,可采用弱還原焰燒成。燒成以后的冷卻階段,600℃以上可以快冷,600℃以下應(yīng)緩慢冷卻。燒成升溫速度(參考值)如下:
燒制硅磚溫度變化表
新聞推薦
產(chǎn)品推薦